పేలవమైన నీటి నిరోధకత, అసమాన ఉపరితలం, అధిక పొడి కంటెంట్ మరియు అసమాన పొడవు? జల ఆహార ఉత్పత్తిలో సాధారణ సమస్యలు మరియు మెరుగుదల చర్యలు
మా రోజువారీ జల ఆహార ఉత్పత్తిలో, మేము వివిధ కోణాల నుండి కొన్ని సమస్యలను ఎదుర్కొన్నాము. అందరితో చర్చించడానికి ఇక్కడ కొన్ని ఉదాహరణలు ఉన్నాయి, అవి ఈ క్రింది విధంగా ఉన్నాయి:
1, ఫార్ములా
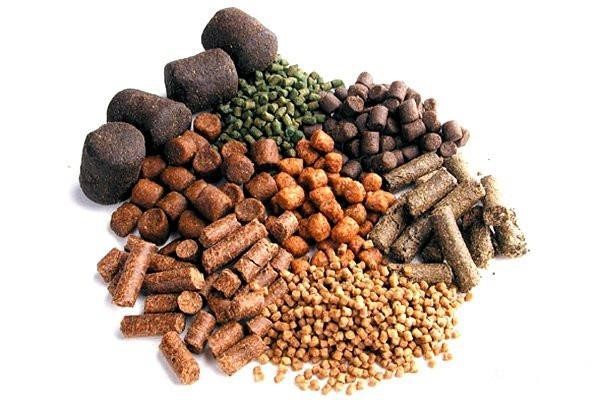
1. చేపల మేత యొక్క ఫార్ములా నిర్మాణంలో, రాప్సీడ్ మీల్, కాటన్ మీల్ మొదలైన ముడి ఫైబర్కు చెందిన మరిన్ని రకాల మీల్ ముడి పదార్థాలు ఉన్నాయి. కొన్ని నూనె కర్మాగారాలు అధునాతన సాంకేతికతను కలిగి ఉంటాయి మరియు నూనెను ప్రాథమికంగా చాలా తక్కువ కంటెంట్తో పొడిగా వేయించాలి. అంతేకాకుండా, ఈ రకమైన ముడి పదార్థాలు ఉత్పత్తిలో సులభంగా శోషించబడవు, ఇది గ్రాన్యులేషన్పై చాలా ప్రభావాన్ని చూపుతుంది. అదనంగా, పత్తి పిండిని చూర్ణం చేయడం కష్టం, ఇది సామర్థ్యాన్ని ప్రభావితం చేస్తుంది.
2. పరిష్కారం: రాప్సీడ్ కేక్ వాడకం పెరిగింది మరియు బియ్యం ఊక వంటి అధిక-నాణ్యత గల స్థానిక పదార్థాలను ఫార్ములాకు జోడించారు. అదనంగా, ఫార్ములాలో దాదాపు 5-8% వాటా కలిగిన గోధుమలను జోడించారు. సర్దుబాటు ద్వారా, 2009లో గ్రాన్యులేషన్ ప్రభావం సాపేక్షంగా ఆదర్శంగా ఉంది మరియు టన్నుకు దిగుబడి కూడా పెరిగింది. 2.5mm కణాలు 8-9 టన్నుల మధ్య ఉన్నాయి, గతంతో పోలిస్తే దాదాపు 2 టన్నుల పెరుగుదల. కణాల రూపాన్ని కూడా గణనీయంగా మెరుగుపరిచారు.
అదనంగా, పత్తి గింజల పిండిని చూర్ణం చేసే సామర్థ్యాన్ని మెరుగుపరచడానికి, మేము పత్తి గింజల పిండిని మరియు రాప్సీడ్ పిండిని 2:1 నిష్పత్తిలో కలిపి నలిపివేశాము. మెరుగుపడిన తర్వాత, క్రషింగ్ వేగం ప్రాథమికంగా రాప్సీడ్ పిండి యొక్క క్రషింగ్ వేగంతో సమానంగా ఉంది.
2, కణాల అసమాన ఉపరితలం
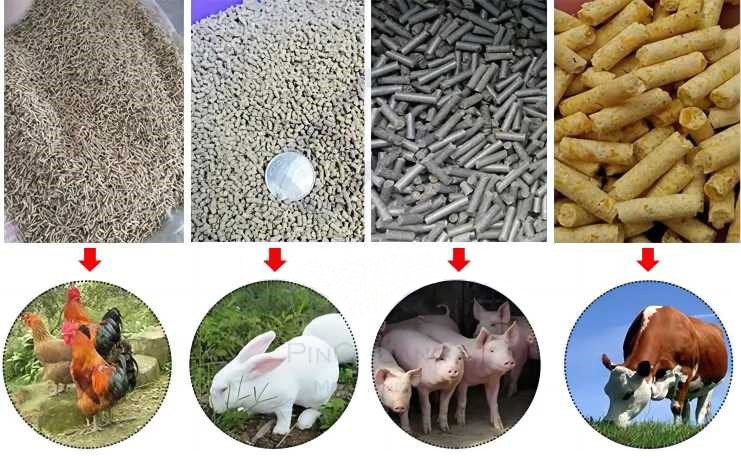
1. ఇది తుది ఉత్పత్తి యొక్క రూపాన్ని బాగా ప్రభావితం చేస్తుంది మరియు నీటిలో కలిపినప్పుడు, అది కూలిపోయే అవకాశం ఉంది మరియు తక్కువ వినియోగ రేటును కలిగి ఉంటుంది. ప్రధాన కారణం:
(1) ముడి పదార్థాలు చాలా ముతకగా చూర్ణం చేయబడతాయి మరియు టెంపరింగ్ ప్రక్రియలో, అవి పూర్తిగా పరిపక్వం చెందవు మరియు మృదువుగా ఉండవు మరియు అచ్చు రంధ్రాల గుండా వెళుతున్నప్పుడు ఇతర ముడి పదార్థాలతో బాగా కలపబడవు.
(2) ముడి ఫైబర్ అధికంగా ఉండే చేపల మేత సూత్రంలో, టెంపరింగ్ ప్రక్రియలో ముడి పదార్థంలో ఆవిరి బుడగలు ఉండటం వల్ల, కణ కుదింపు సమయంలో అచ్చు లోపల మరియు వెలుపల ఒత్తిడి వ్యత్యాసం కారణంగా ఈ బుడగలు పగిలిపోతాయి, ఫలితంగా కణాల ఉపరితలం అసమానంగా ఉంటుంది.
2. నిర్వహణ చర్యలు:
(1) క్రషింగ్ ప్రక్రియను సరిగ్గా నియంత్రించండి
ప్రస్తుతం, చేపల దాణాను ఉత్పత్తి చేసేటప్పుడు, మా కంపెనీ 1.2mm జల్లెడ మైక్రో పౌడర్ను బల్క్ ముడి పదార్థంగా ఉపయోగిస్తుంది. చూర్ణం యొక్క సున్నితమైనత్వాన్ని నిర్ధారించడానికి మేము జల్లెడ యొక్క వాడకం యొక్క ఫ్రీక్వెన్సీని మరియు సుత్తి యొక్క దుస్తులు స్థాయిని నియంత్రిస్తాము.
(2) ఆవిరి పీడనాన్ని నియంత్రించండి
ఫార్ములా ప్రకారం, ఉత్పత్తి సమయంలో ఆవిరి పీడనాన్ని సహేతుకంగా సర్దుబాటు చేయండి, సాధారణంగా 0.2 చుట్టూ నియంత్రిస్తుంది. చేపల మేత సూత్రంలో పెద్ద మొత్తంలో ముతక ఫైబర్ ముడి పదార్థాలు ఉన్నందున, అధిక-నాణ్యత ఆవిరి మరియు సహేతుకమైన టెంపరింగ్ సమయం అవసరం.
3, కణాల నీటి నిరోధకత తక్కువగా ఉండటం.
1. ఈ రకమైన సమస్య మన రోజువారీ ఉత్పత్తిలో సర్వసాధారణం, సాధారణంగా ఈ క్రింది అంశాలకు సంబంధించినది:
(1) తక్కువ టెంపరింగ్ సమయం మరియు తక్కువ టెంపరింగ్ ఉష్ణోగ్రత అసమానంగా లేదా తగినంత టెంపరింగ్ లేకపోవడం, తక్కువ పక్వానికి వచ్చే స్థాయి మరియు తగినంత తేమ లేకపోవడం వంటి వాటికి దారితీస్తుంది.
(2) స్టార్చ్ వంటి అంటుకునే పదార్థాలు తగినంతగా లేకపోవడం.
(3) రింగ్ అచ్చు యొక్క కుదింపు నిష్పత్తి చాలా తక్కువగా ఉంది.
(4) ఫార్ములాలో నూనె శాతం మరియు ముడి ఫైబర్ ముడి పదార్థాల నిష్పత్తి చాలా ఎక్కువగా ఉన్నాయి.
(5) క్రషింగ్ కణ పరిమాణం కారకం.
2. నిర్వహణ చర్యలు:
(1) ఆవిరి నాణ్యతను మెరుగుపరచడం, నియంత్రకం యొక్క బ్లేడ్ కోణాన్ని సర్దుబాటు చేయడం, టెంపరింగ్ సమయాన్ని పొడిగించడం మరియు ముడి పదార్థాల తేమను తగిన విధంగా పెంచడం.
(2) ఫార్ములాను సర్దుబాటు చేయండి, స్టార్చ్ ముడి పదార్థాలను తగిన విధంగా పెంచండి మరియు కొవ్వు మరియు ముడి ఫైబర్ ముడి పదార్థాల నిష్పత్తిని తగ్గించండి.
(3) అవసరమైతే అంటుకునే పదార్థాన్ని జోడించండి. (సోడియం ఆధారిత బెంటోనైట్ స్లర్రీ)
(4) యొక్క కుదింపు నిష్పత్తిని మెరుగుపరచండిరింగ్ డై
(5) బాగా చూర్ణం చేయడం యొక్క సూక్ష్మతను నియంత్రించండి
4, కణాలలో అధిక పొడి కంటెంట్
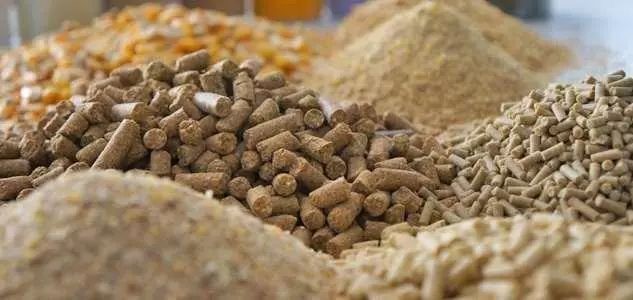
1. శీతలీకరణ తర్వాత మరియు స్క్రీనింగ్ ముందు సాధారణ గుళికల ఫీడ్ రూపాన్ని నిర్ధారించడం కష్టం. గుళికలలో ఎక్కువ చక్కటి బూడిద మరియు పొడి ఉన్నాయని వినియోగదారులు నివేదించారు. పై విశ్లేషణ ఆధారంగా, దీనికి అనేక కారణాలు ఉన్నాయని నేను భావిస్తున్నాను:
ఎ. కణ ఉపరితలం నునుపుగా ఉండదు, కోత చక్కగా ఉండదు మరియు కణాలు వదులుగా ఉంటాయి మరియు పొడి ఉత్పత్తికి గురవుతాయి;
బి. గ్రేడింగ్ స్క్రీన్ ద్వారా అసంపూర్ణ స్క్రీనింగ్, మూసుకుపోయిన స్క్రీన్ మెష్, రబ్బరు బంతుల తీవ్ర అరుగుదల, సరిపోలని స్క్రీన్ మెష్ ఎపర్చరు మొదలైనవి;
సి. తుది ఉత్పత్తి గిడ్డంగిలో చాలా చక్కటి బూడిద అవశేషాలు ఉన్నాయి మరియు క్లియరెన్స్ పూర్తిగా లేదు;
D. ప్యాకేజింగ్ మరియు తూకం వేసేటప్పుడు దుమ్ము తొలగింపులో దాగి ఉన్న ప్రమాదాలు ఉన్నాయి;
నిర్వహణ చర్యలు:
ఎ. ఫార్ములా నిర్మాణాన్ని ఆప్టిమైజ్ చేయండి, రింగ్ డైని సహేతుకంగా ఎంచుకోండి మరియు కంప్రెషన్ నిష్పత్తిని బాగా నియంత్రించండి.
బి. గ్రాన్యులేషన్ ప్రక్రియలో, ముడి పదార్థాలను పూర్తిగా పక్వానికి మరియు మృదువుగా చేయడానికి టెంపరింగ్ సమయం, దాణా పరిమాణం మరియు గ్రాన్యులేషన్ ఉష్ణోగ్రతను నియంత్రించండి.
C. పార్టికల్ క్రాస్-సెక్షన్ చక్కగా ఉందని నిర్ధారించుకోండి మరియు స్టీల్ స్ట్రిప్తో తయారు చేసిన మృదువైన కటింగ్ కత్తిని ఉపయోగించండి.
D. గ్రేడింగ్ స్క్రీన్ను సర్దుబాటు చేయండి మరియు నిర్వహించండి మరియు సహేతుకమైన స్క్రీన్ కాన్ఫిగరేషన్ను ఉపయోగించండి.
E. తుది ఉత్పత్తి గిడ్డంగి కింద సెకండరీ స్క్రీనింగ్ టెక్నాలజీని ఉపయోగించడం వల్ల పౌడర్ కంటెంట్ నిష్పత్తి బాగా తగ్గుతుంది.
F. తుది ఉత్పత్తి గిడ్డంగి మరియు సర్క్యూట్ను సకాలంలో శుభ్రం చేయడం అవసరం. అదనంగా, ప్యాకేజింగ్ మరియు దుమ్ము తొలగింపు పరికరాన్ని మెరుగుపరచడం అవసరం. దుమ్ము తొలగింపు కోసం ప్రతికూల ఒత్తిడిని ఉపయోగించడం ఉత్తమం, ఇది మరింత ఆదర్శవంతమైనది. ముఖ్యంగా ప్యాకేజింగ్ ప్రక్రియలో, ప్యాకేజింగ్ కార్మికుడు క్రమం తప్పకుండా ప్యాకేజింగ్ స్కేల్ యొక్క బఫర్ హాప్పర్ నుండి దుమ్మును తట్టి శుభ్రం చేయాలి..
5, కణ పొడవు మారుతూ ఉంటుంది
1. రోజువారీ ఉత్పత్తిలో, ముఖ్యంగా 420 కంటే ఎక్కువ మోడళ్లకు నియంత్రణలో మనం తరచుగా ఇబ్బందులను ఎదుర్కొంటాము. దీనికి గల కారణాలను ఈ క్రింది విధంగా సంగ్రహించవచ్చు:
(1) గ్రాన్యులేషన్ కోసం దాణా మొత్తం అసమానంగా ఉంటుంది మరియు టెంపరింగ్ ప్రభావం చాలా హెచ్చుతగ్గులకు లోనవుతుంది.
(2) అచ్చు రోలర్ల మధ్య అస్థిరమైన అంతరం లేదా రింగ్ అచ్చు మరియు ప్రెజర్ రోలర్ల తీవ్ర దుస్తులు.
(3) రింగ్ అచ్చు యొక్క అక్షసంబంధ దిశలో, రెండు చివర్లలో ఉత్సర్గ వేగం మధ్యలో కంటే తక్కువగా ఉంటుంది.
(4) రింగ్ అచ్చు యొక్క పీడన తగ్గింపు రంధ్రం చాలా పెద్దది మరియు ప్రారంభ రేటు చాలా ఎక్కువగా ఉంటుంది.
(5) కటింగ్ బ్లేడ్ యొక్క స్థానం మరియు కోణం అసమంజసమైనవి.
(6) గ్రాన్యులేషన్ ఉష్ణోగ్రత.
(7) రింగ్ డై కటింగ్ బ్లేడ్ రకం మరియు ప్రభావవంతమైన ఎత్తు (బ్లేడ్ వెడల్పు, వెడల్పు) ప్రభావం చూపుతాయి.
(8) అదే సమయంలో, కంప్రెషన్ చాంబర్ లోపల ముడి పదార్థాల పంపిణీ అసమానంగా ఉంటుంది.
2. ఫీడ్ మరియు గుళికల నాణ్యతను సాధారణంగా వాటి అంతర్గత మరియు బాహ్య లక్షణాల ఆధారంగా విశ్లేషిస్తారు. ఉత్పత్తి వ్యవస్థగా, ఫీడ్ గుళికల బాహ్య నాణ్యతకు సంబంధించిన విషయాలకు మనం ఎక్కువగా గురవుతాము. ఉత్పత్తి దృక్కోణం నుండి, జల ఫీడ్ గుళికల నాణ్యతను ప్రభావితం చేసే అంశాలను సుమారుగా ఈ క్రింది విధంగా సంగ్రహించవచ్చు:
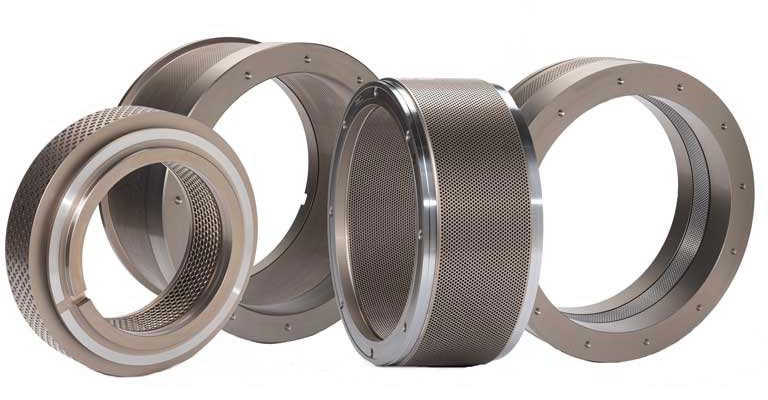
(1) ఫార్ములాల రూపకల్పన మరియు నిర్వహణ జల ఫీడ్ గుళికల నాణ్యతపై ప్రత్యక్ష ప్రభావాన్ని చూపుతాయి, మొత్తంలో దాదాపు 40% వాటా కలిగి ఉంటాయి;
(2) అణిచివేత తీవ్రత మరియు కణ పరిమాణం యొక్క ఏకరూపత;
(3) రింగ్ అచ్చు యొక్క వ్యాసం, కుదింపు నిష్పత్తి మరియు సరళ వేగం కణాల పొడవు మరియు వ్యాసంపై ప్రభావం చూపుతాయి;
(4) రింగ్ అచ్చు యొక్క కుదింపు నిష్పత్తి, సరళ వేగం, చల్లార్చు మరియు టెంపరింగ్ ప్రభావం మరియు కణాల పొడవుపై కటింగ్ బ్లేడ్ ప్రభావం;
(5) ముడి పదార్థాల తేమ శాతం, టెంపరింగ్ ప్రభావం, చల్లబరచడం మరియు ఎండబెట్టడం వంటివి తుది ఉత్పత్తుల తేమ శాతం మరియు రూపాన్ని ప్రభావితం చేస్తాయి;
(6) పరికరాలు, ప్రక్రియ కారకాలు మరియు క్వెన్చింగ్ మరియు టెంపరింగ్ ప్రభావాలు కణ పొడి కంటెంట్పై ప్రభావం చూపుతాయి;
3. నిర్వహణ చర్యలు:
(1) ఫాబ్రిక్ స్క్రాపర్ యొక్క పొడవు, వెడల్పు మరియు కోణాన్ని సర్దుబాటు చేయండి మరియు అరిగిపోయిన స్క్రాపర్ను భర్తీ చేయండి.
(2) తక్కువ మొత్తంలో ఫీడింగ్ కారణంగా ఉత్పత్తి ప్రారంభంలో మరియు ముగింపులో కటింగ్ బ్లేడ్ స్థానాన్ని సకాలంలో సర్దుబాటు చేయడంపై శ్రద్ధ వహించండి.
(3) ఉత్పత్తి ప్రక్రియలో, స్థిరమైన దాణా రేటు మరియు ఆవిరి సరఫరాను నిర్ధారించుకోండి. ఆవిరి పీడనం తక్కువగా ఉండి ఉష్ణోగ్రత పెరగలేకపోతే, దానిని సకాలంలో సర్దుబాటు చేయాలి లేదా ఆపాలి.
(4) మధ్య అంతరాన్ని సహేతుకంగా సర్దుబాటు చేయండిరోలర్ షెల్. కొత్త రోలర్లతో కొత్త అచ్చును అనుసరించండి మరియు ప్రెజర్ రోలర్ మరియు రింగ్ అచ్చు యొక్క అసమాన ఉపరితలాన్ని ధరించడం వల్ల వెంటనే మరమ్మతు చేయండి.
(5) రింగ్ అచ్చు యొక్క గైడ్ రంధ్రాన్ని మరమ్మతు చేయండి మరియు మూసుకుపోయిన అచ్చు రంధ్రాన్ని వెంటనే శుభ్రం చేయండి.
(6) రింగ్ అచ్చును ఆర్డర్ చేసేటప్పుడు, అసలు రింగ్ అచ్చు యొక్క అక్షసంబంధ దిశ యొక్క రెండు చివర్లలోని మూడు వరుసల రంధ్రాల కుదింపు నిష్పత్తి మధ్యలో ఉన్న దాని కంటే 1-2 మిమీ తక్కువగా ఉండవచ్చు.
(7) రింగ్ అచ్చు మరియు ప్రెజర్ రోలర్ మధ్య మెషింగ్ లైన్లో ఉండేలా వీలైనంత వరకు పదునైన అంచు ఉండేలా, 0.5-1 మిమీ మందం నియంత్రించబడే మృదువైన కటింగ్ కత్తిని ఉపయోగించండి.
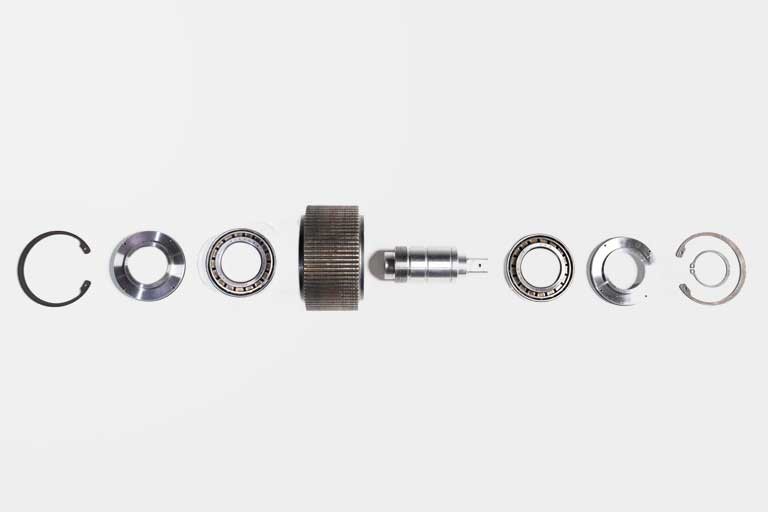
(8) రింగ్ అచ్చు యొక్క కేంద్రీకరణను నిర్ధారించండి, గ్రాన్యులేటర్ యొక్క స్పిండిల్ క్లియరెన్స్ను క్రమం తప్పకుండా తనిఖీ చేయండి మరియు అవసరమైతే దాన్ని సర్దుబాటు చేయండి.
6, సారాంశం నియంత్రణ పాయింట్లు:
1. గ్రైండింగ్: గ్రైండింగ్ యొక్క సూక్ష్మతను స్పెసిఫికేషన్ అవసరాలకు అనుగుణంగా నియంత్రించాలి.
2. మిక్సింగ్: తగిన మిక్సింగ్ పరిమాణం, మిక్సింగ్ సమయం, తేమ శాతం మరియు ఉష్ణోగ్రత ఉండేలా ముడి పదార్థాల మిక్సింగ్ యొక్క ఏకరూపతను నియంత్రించాలి.
3. పరిపక్వత: పఫింగ్ యంత్రం యొక్క పీడనం, ఉష్ణోగ్రత మరియు తేమను నియంత్రించాలి.
కణ పదార్థం యొక్క పరిమాణం మరియు ఆకారం: కంప్రెషన్ అచ్చులు మరియు కటింగ్ బ్లేడ్ల యొక్క తగిన స్పెసిఫికేషన్లను ఎంచుకోవాలి.
5. పూర్తయిన దాణాలో నీటి శాతం: ఎండబెట్టడం మరియు చల్లబరచడం సమయం మరియు ఉష్ణోగ్రతను నిర్ధారించుకోవడం అవసరం.
6. ఆయిల్ స్ప్రేయింగ్: ఆయిల్ స్ప్రేయింగ్ యొక్క ఖచ్చితమైన మొత్తం, నాజిల్ల సంఖ్య మరియు నూనె నాణ్యతను నియంత్రించడం అవసరం.
7. స్క్రీనింగ్: పదార్థం యొక్క స్పెసిఫికేషన్ల ప్రకారం జల్లెడ పరిమాణాన్ని ఎంచుకోండి.
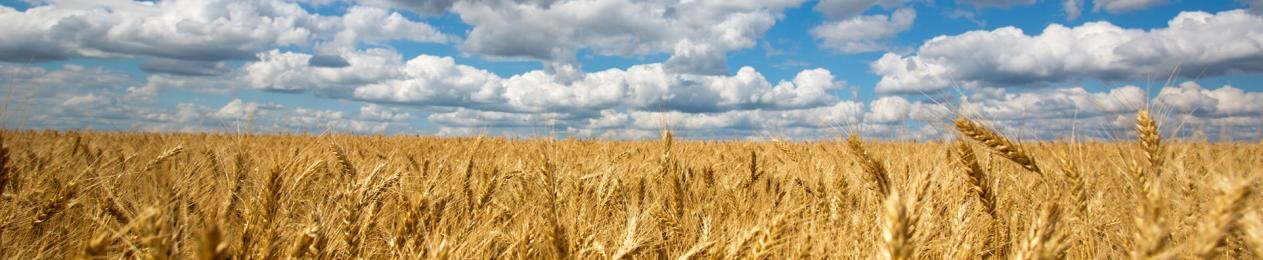
పోస్ట్ సమయం: నవంబర్-30-2023